Tesla cars are renowned for their advanced technology, sleek design, and high performance. But have you ever wondered how these state-of-the-art electric vehicles are actually made? From the initial design stages to the final assembly, the production of a Tesla car is a fascinating process that combines cutting-edge technology with traditional manufacturing techniques.
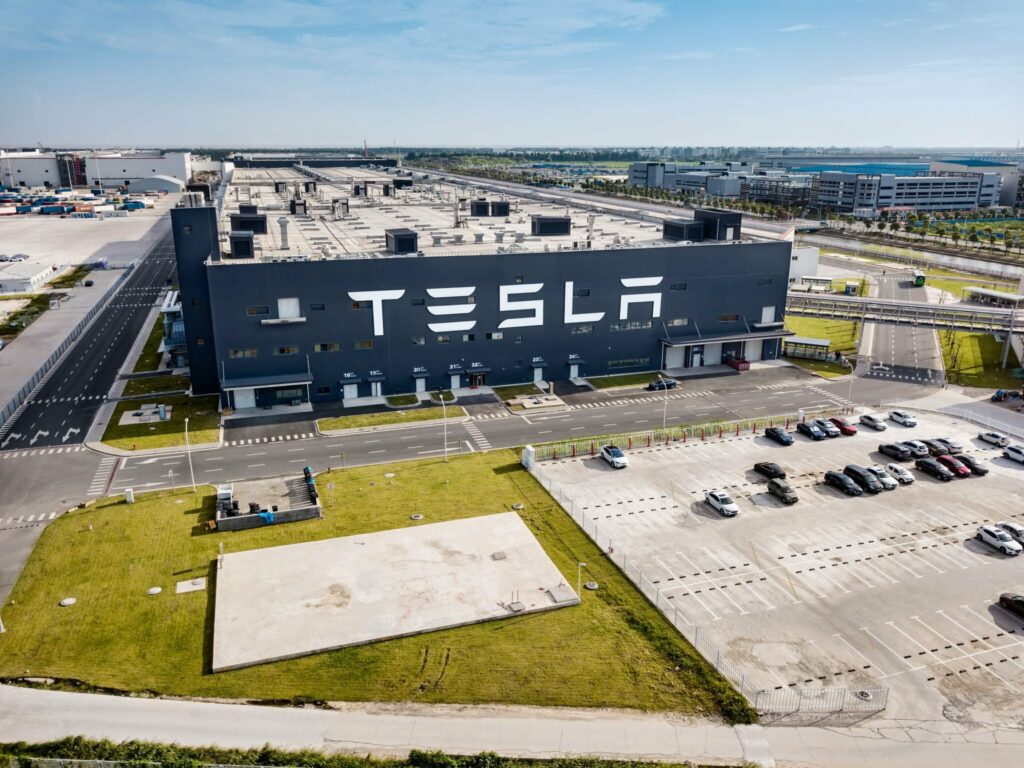
Table of Contents
The Making of Tesla Cars
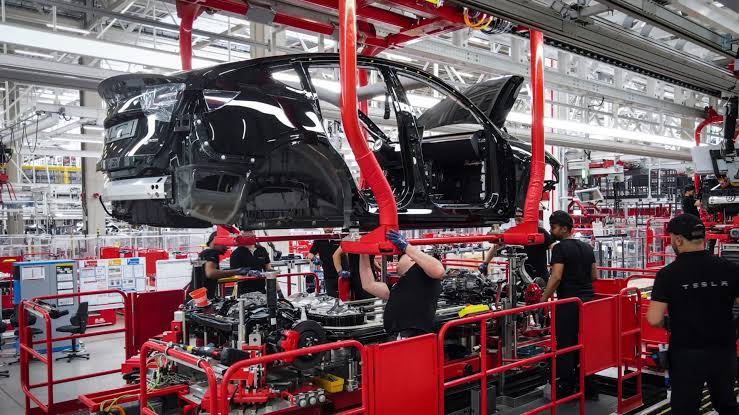
The first step in the production of a Tesla car is the design phase. Tesla’s team of engineers and designers work meticulously to create a blueprint for each vehicle, carefully considering factors such as aerodynamics, safety, and aesthetics. The design is then brought to life through computer simulations and 3D modeling, allowing the team to refine every detail before the car goes into production.
Once the design is finalized, the production process begins at Tesla’s state-of-the-art manufacturing facilities. The raw materials used to build a Tesla car are sourced from suppliers around the world and include items such as steel, aluminum, and lithium-ion batteries. These materials are then brought to the production line, where they undergo various processes to transform them into the components that make up the car.
One of the key components of a Tesla car is its battery pack. Tesla’s advanced battery technology is at the heart of its electric vehicles, providing power and range that surpasses traditional internal combustion engine vehicles. The battery pack is assembled using thousands of individual battery cells, which are carefully arranged and connected to create a powerful and efficient energy storage system.
In addition to the battery pack, a Tesla car also features a lightweight and durable aluminum chassis, which is manufactured using advanced forming and welding techniques. The chassis is then combined with other components such as the motor, drivetrain, and suspension to create the vehicle’s basic structure.
The interior of a Tesla car is also carefully crafted, with a focus on comfort, convenience, and cutting-edge technology. High-quality materials such as premium leather, sustainable wood, and carbon fiber are used to create a luxurious and modern interior that meets Tesla’s high standards for design and functionality.
Finally, all the components of the Tesla car come together on the assembly line, where skilled technicians meticulously put the vehicle together. The assembly process involves thousands of individual steps, from installing electric wiring and connecting components to fitting body panels and performing quality checks.
Throughout the production process, Tesla utilizes advanced robotics and automation to streamline production and ensure precision and quality in every vehicle. However, the company also recognizes the importance of skilled human labor in the manufacturing process and maintains a workforce of highly trained technicians to oversee the production of each car.
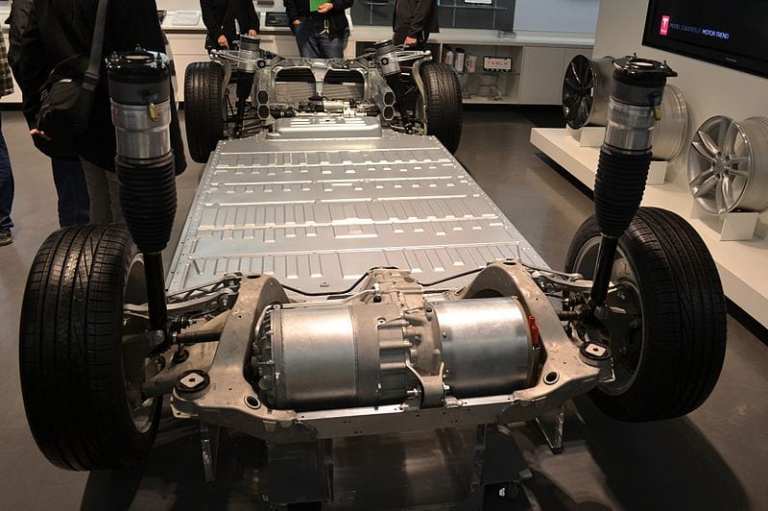
The production of a Tesla car is a complex and intricate process that involves cutting-edge technology, advanced manufacturing techniques, and skilled craftsmanship. From the initial design stages to the final assembly, every step of the production process is carefully orchestrated to create a vehicle that embodies Tesla’s commitment to innovation, sustainability, and excellence.
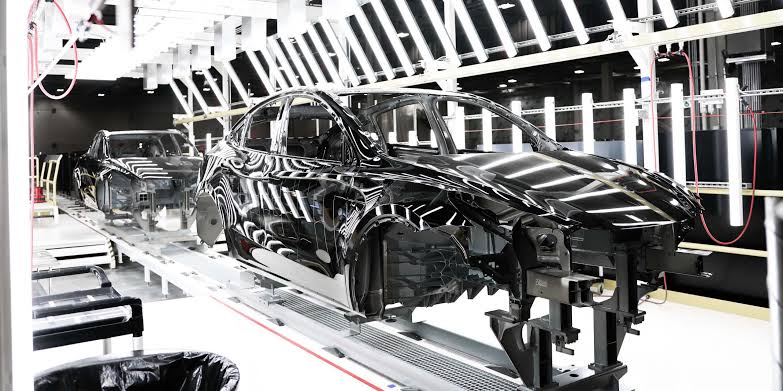
Tesla has released a series of innovative and sleek car models that have redefined the concept of eco-friendly driving.
A list of Tesla cars models released until now
1. Tesla Roadster: The Roadster was Tesla’s first production car and became the first highway-legal all-electric sports car. It was introduced in 2008 and had a range of 245 miles on a single charge.
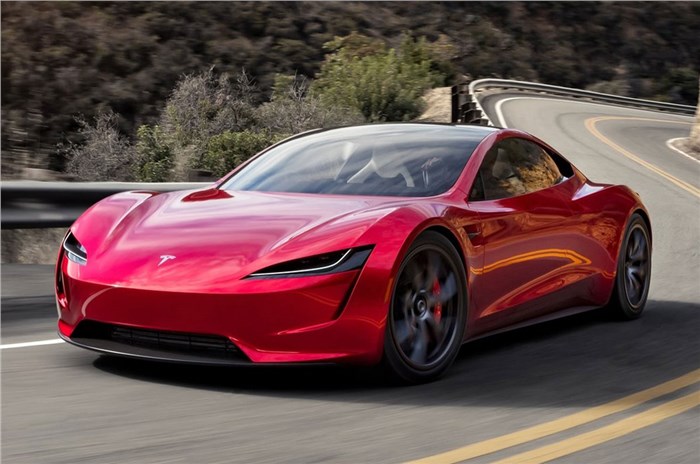
2. Tesla Model S: The Model S is a full-sized all-electric luxury sedan that has been acclaimed for its performance, safety, and range. It was launched in 2012 and has set new standards for electric vehicles.
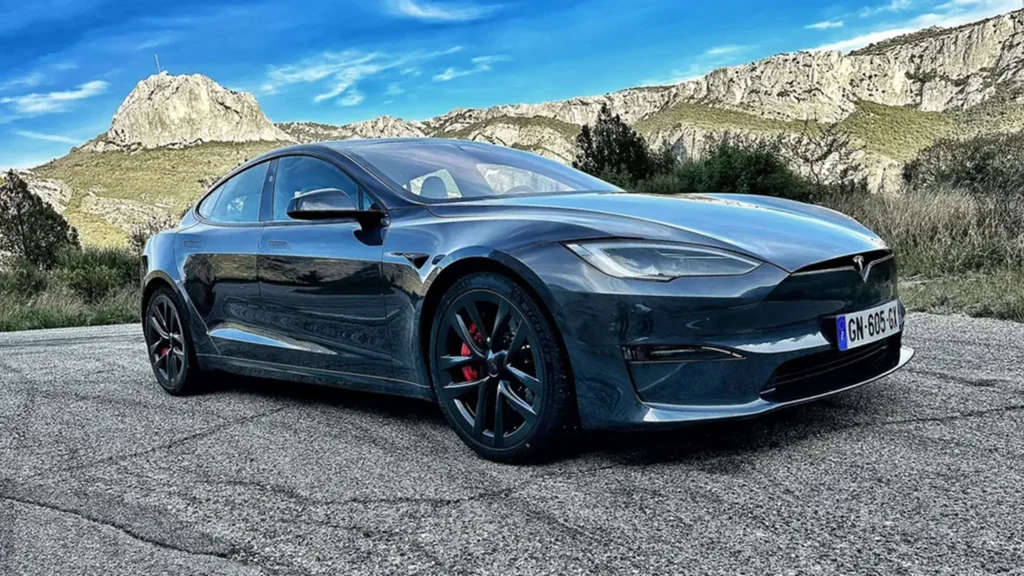
3. Tesla Model X: The Model X is an all-electric luxury SUV that was introduced in 2015. It is known for its falcon-wing doors and impressive performance capabilities.

4. Tesla Model 3: The Model 3 is a more affordable electric sedan and is Tesla’s best-selling vehicle. It was unveiled in 2016 and has gained popularity for its practicality and performance.
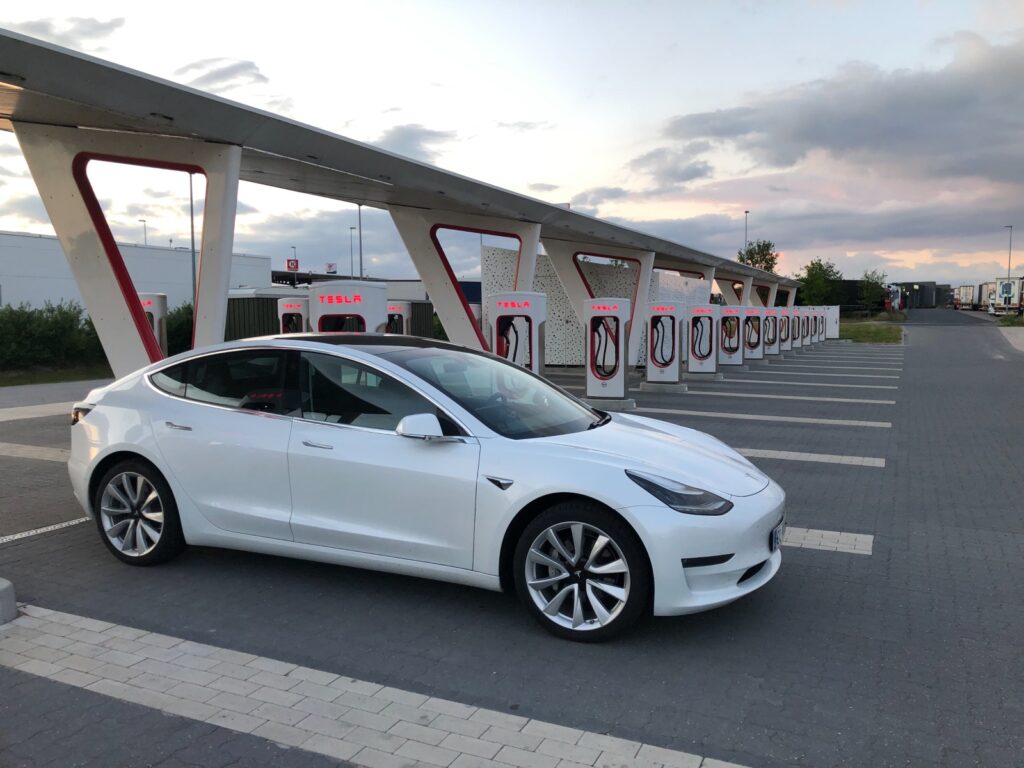
5. Tesla Model Y: The Model Y is an all-electric compact crossover that was launched in 2020. It shares many components with the Model 3 and offers more space and versatility for drivers.
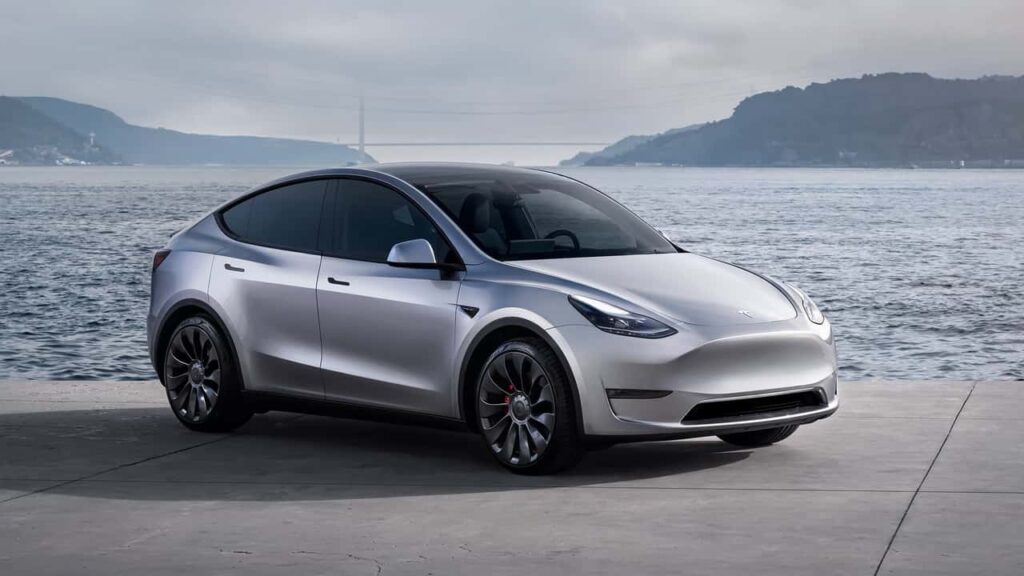
6. Tesla Cybertruck: The Cybertruck is an upcoming all-electric pickup truck that was unveiled in 2019. Its unconventional and futuristic design has garnered widespread attention and anticipation.
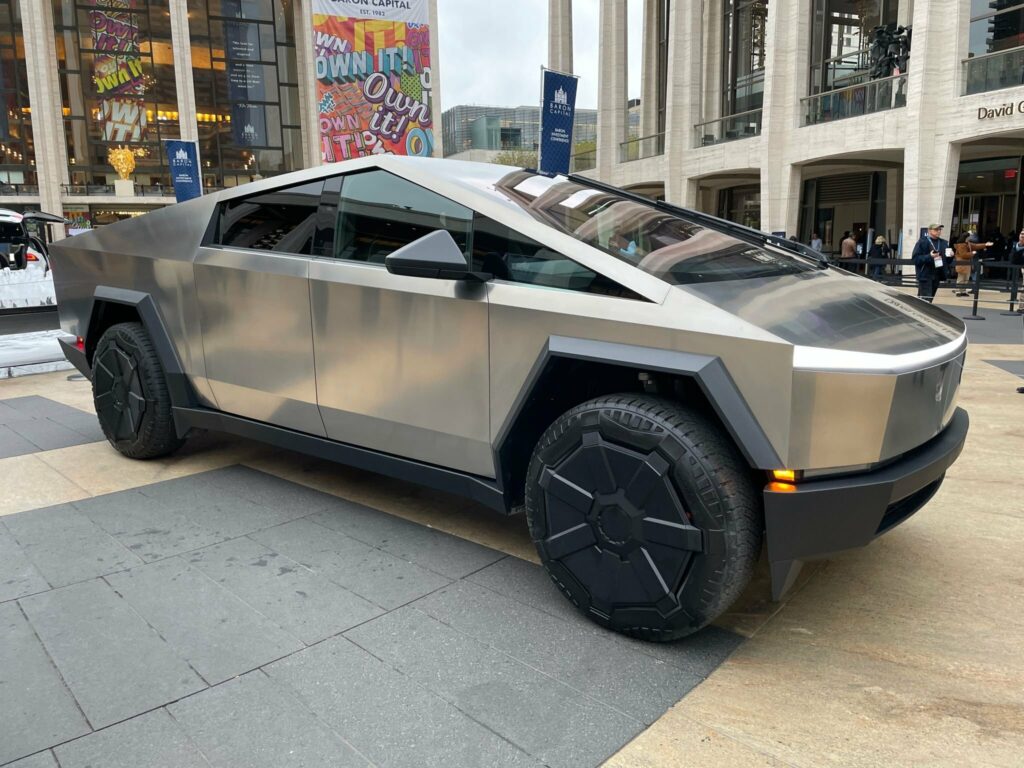
7. Tesla Semi: The Tesla Semi is an upcoming all-electric battery-powered Class 8 semi-truck that is designed for long-haul transportation. It is expected to enter production in the near future.
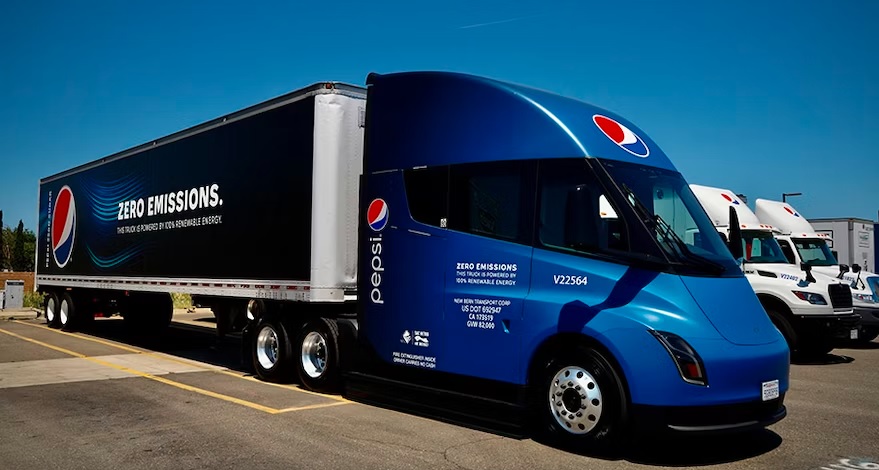
8. Tesla Roadster 2024 (upcoming): Tesla has also announced a second-generation Roadster, which is set to be the fastest production car in the world. It is expected to be released in the near future.
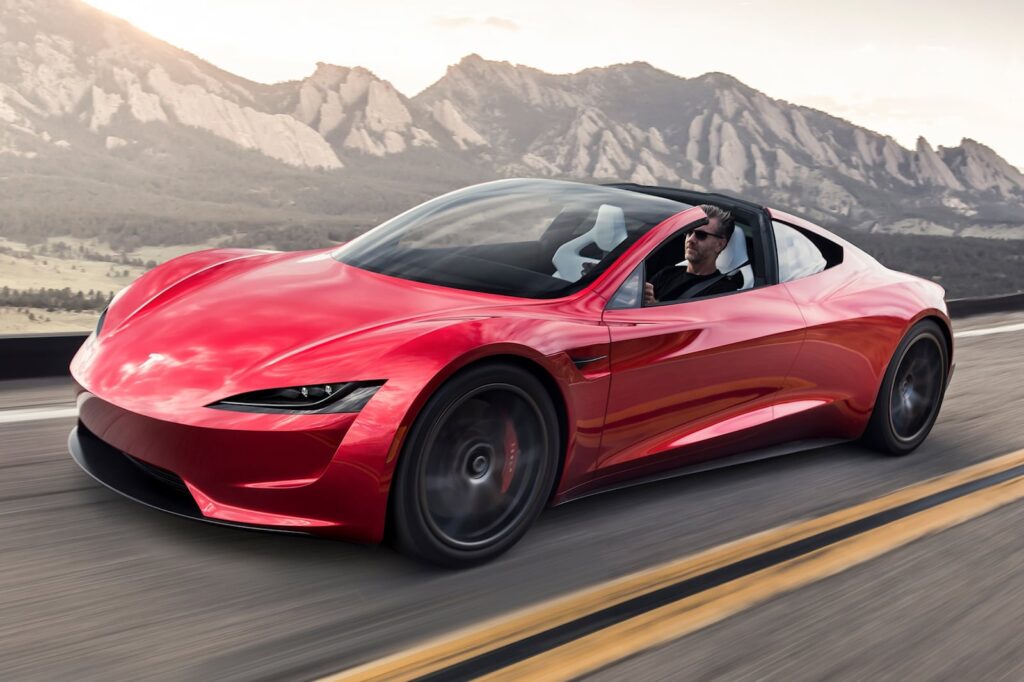
Tesla’s commitment to innovation and sustainable transportation has resulted in a diverse range of cutting-edge electric vehicles. With each new release, the company continues to push the boundaries of what is possible in the electric car market, making eco-friendly driving more accessible and exciting than ever. As Tesla continues to expand and innovate, there is no doubt that the future holds even more revolutionary car models from this trailblazing company.
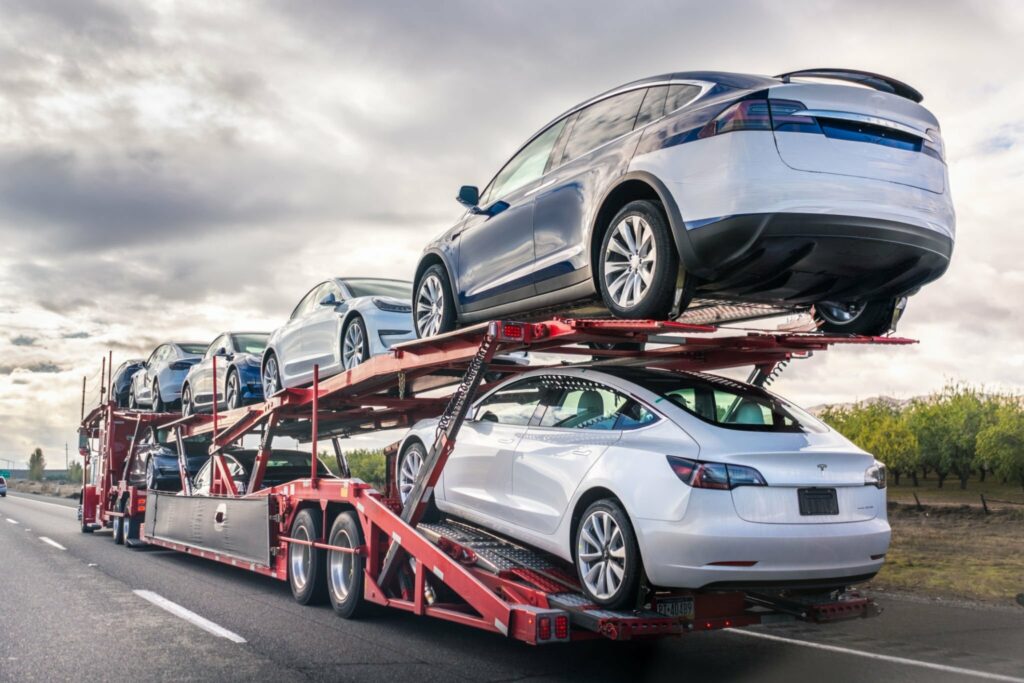
The components and materials used in the production of Tesla cars include:
- Lithium-ion batteries: These are used to power the electric motors in Tesla cars.
- Aluminum: The body of Tesla cars is made mostly of aluminum, which is lightweight and strong.
- High-strength steel: This material is used to provide structural integrity and safety in Tesla cars.
- Carbon fiber: This lightweight and strong material is used in some components of Tesla cars to help reduce weight and improve performance.
- Glass: Tesla cars feature panoramic glass roofs and other glass components.
- Electronics and software: Tesla cars are equipped with advanced electronics and software systems to control the electric motors, battery management, and other functions.
- Interior materials: Tesla cars feature high-quality interior materials such as leather, wood, and premium fabrics.
- Other components: Various other materials and components are used in the production of Tesla cars, including rubber, plastic, and various other metals and alloys.
The key steps and processes involved in the manufacturing of Tesla cars from start to finish include:
- Raw Material Procurement: Tesla sources raw materials such as steel, aluminum, and lithium for battery production from various suppliers.
- Component Manufacturing: Tesla manufactures core components of their cars such as motors, battery packs, and the body frame in-house.
- Assembly Line: The various components are assembled on the production line with the help of advanced robotics and automated systems.
- Quality Control: Each car goes through rigorous quality control checks to ensure that it meets Tesla’s standards for safety and performance.
- Testing and Validation: Once the car is assembled, it undergoes extensive testing and validation processes to ensure that it meets regulatory and safety standards.
- Final Inspection: The fully assembled car is inspected for any defects and undergoes a final quality check before it is ready for delivery.
- Delivery: Once the car passes all the quality checks, it is ready for delivery to the customer.
Throughout these processes, Tesla emphasizes sustainability and efficiency, utilizing renewable energy sources and implementing eco-friendly manufacturing practices. The company also continuously innovates its manufacturing processes to improve quality and decrease production costs.
The Battery Packs in Tesla Cars
With the rise of electric vehicles in the automotive industry, one of the key components that make these vehicles possible is the battery pack. In the case of Tesla’s Model S and Model X, the battery packs contain thousands of 18650-type cylindrical lithium-ion battery cells with nickel-cobalt-aluminum cathodes.
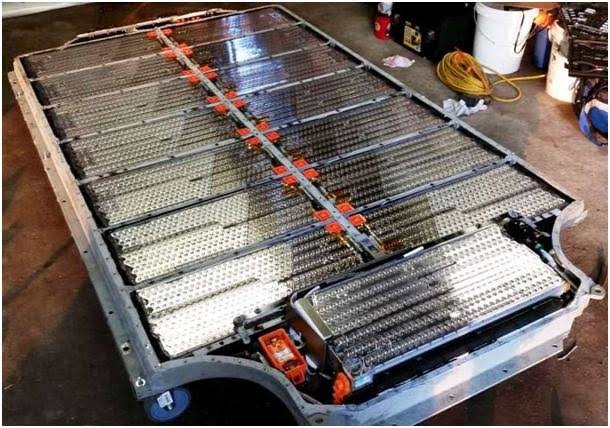
The 18650-type cylindrical lithium-ion battery cells are a popular choice for electric vehicles due to their high energy density and relatively low weight. These cells are small and lightweight, allowing for a higher number to be packed into the battery pack, which ultimately results in a longer driving range.
The nickel-cobalt-aluminum cathodes in these battery cells also play a crucial role in their performance. This particular cathode material is known for its high energy density, which means that it can store a large amount of energy in a relatively small space. This is essential for electric vehicles as it allows them to travel longer distances on a single charge.
The use of nickel in the cathode provides stability and durability to the battery cells, allowing them to withstand the rigors of daily use in an electric vehicle. Meanwhile, the aluminum component helps to enhance the longevity and efficiency of the battery cells.
The combination of these advanced battery cells and cathode materials in the Model S and Model X battery packs is what allows these electric vehicles to achieve impressive driving ranges and high performance. It also sets the standard for the future of electric vehicles, as automakers continue to develop and improve the technology behind their battery packs.
In addition to the technical aspects, the use of these advanced battery cells also contributes to the overall sustainability of electric vehicles. With a longer lifespan and higher energy density, the 18650-type cylindrical lithium-ion battery cells with nickel-cobalt-aluminum cathodes reduce the environmental impact of electric vehicles compared to traditional gasoline-powered cars.
The battery packs in the Model S and Model X represent a significant advancement in electric vehicle technology. Their use of thousands of 18650-type cylindrical lithium-ion battery cells with nickel-cobalt-aluminum cathodes is a testament to Tesla’s commitment to pushing the boundaries of what is possible in the electric vehicle industry. As the demand for electric vehicles continues to grow, it is likely that we will see further developments in battery technology that will continue to improve the performance and sustainability of electric vehicles in the future.
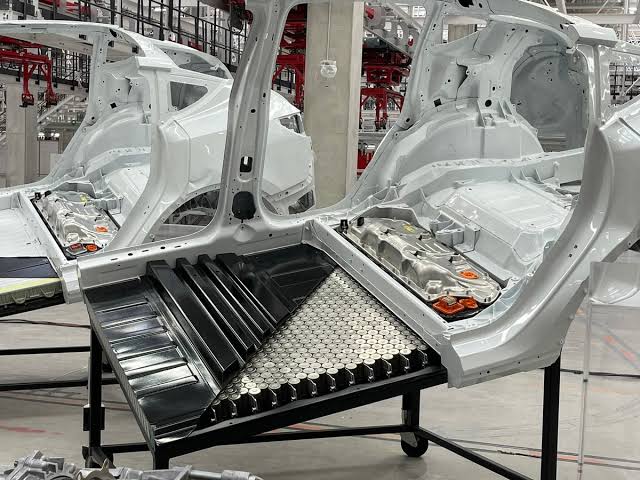
The Tesla Fremont Factory
The Tesla Fremont Factory, located in Fremont, California, is a state-of-the-art manufacturing facility that serves as the primary production site for Tesla’s electric vehicles. The factory is one of the largest manufacturing plants in the world, covering over 5.3 million square feet and employing thousands of workers.
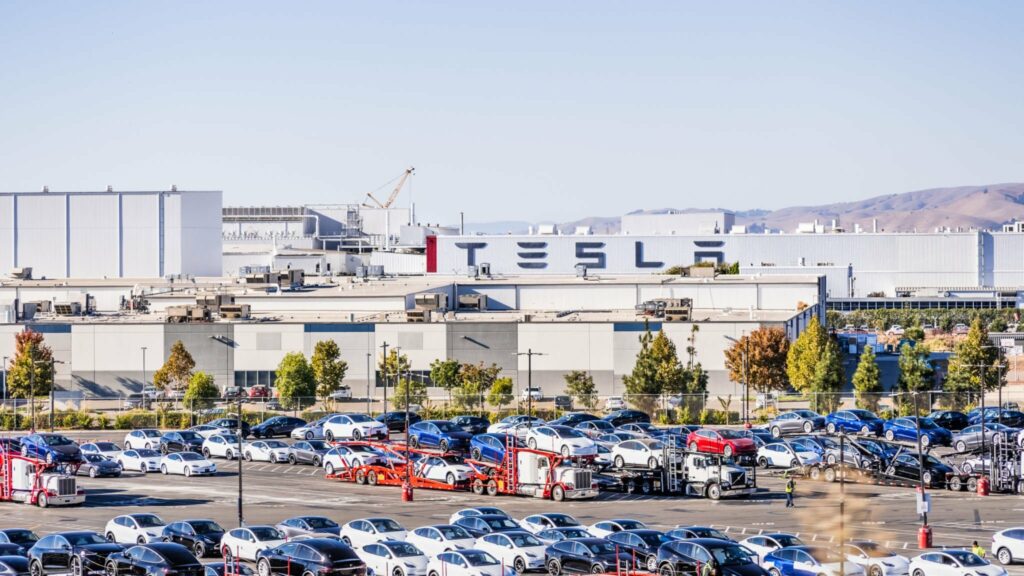
The Fremont Factory was originally built by General Motors in 1962 and was later operated jointly by General Motors and Toyota. In 2010, Tesla acquired the factory and began the process of retooling it for electric vehicle production. Since then, the facility has been a key component in Tesla’s ambitious plans to revolutionize the automotive industry with its line of electric cars.
The factory is best known for producing the Tesla Model S, Model X, Model 3, and Model Y. These vehicles have garnered widespread acclaim for their cutting-edge technology, impressive performance, and sleek design. The Fremont Factory is capable of producing over 500,000 vehicles per year, making it one of the most prolific car manufacturing plants in the world.
What sets the Tesla Fremont Factory apart from traditional automotive manufacturing plants is its commitment to sustainability and innovation. The factory is powered by renewable energy sources, including a large solar panel installation and on-site battery storage. This allows Tesla to significantly reduce its carbon footprint and operate in an environmentally responsible manner.
In addition to its focus on sustainability, the Fremont Factory is also at the forefront of advanced manufacturing techniques. The facility utilizes state-of-the-art robotics, automation, and artificial intelligence to streamline production processes and increase efficiency. This allows Tesla to manufacture high-quality vehicles at a rapid pace while maintaining strict quality control standards.
The Fremont Factory has also become a center for research and development, with Tesla dedicating significant resources to advancing battery technology, vehicle design, and manufacturing processes. This commitment to innovation has contributed to the company’s position as a leader in the electric vehicle industry.
In recent years, the Fremont Factory has faced its share of challenges, including production bottlenecks, labor disputes, and regulatory issues. However, Tesla has continued to invest in the facility and implement improvements to address these challenges, ensuring that the factory remains a key asset in the company’s long-term growth strategy.
Looking ahead, the Tesla Fremont Factory is poised to play an even bigger role in the company’s future. With the introduction of new vehicle models, such as the highly anticipated Tesla Cybertruck and the Tesla Semi, the factory will be instrumental in meeting the growing demand for electric vehicles and expanding Tesla’s global reach.
The Tesla Fremont Factory stands as a shining example of the potential of sustainable, high-tech manufacturing. With its focus on innovation, quality, and efficiency, the factory is at the forefront of the electric vehicle revolution and is helping to shape the future of transportation.
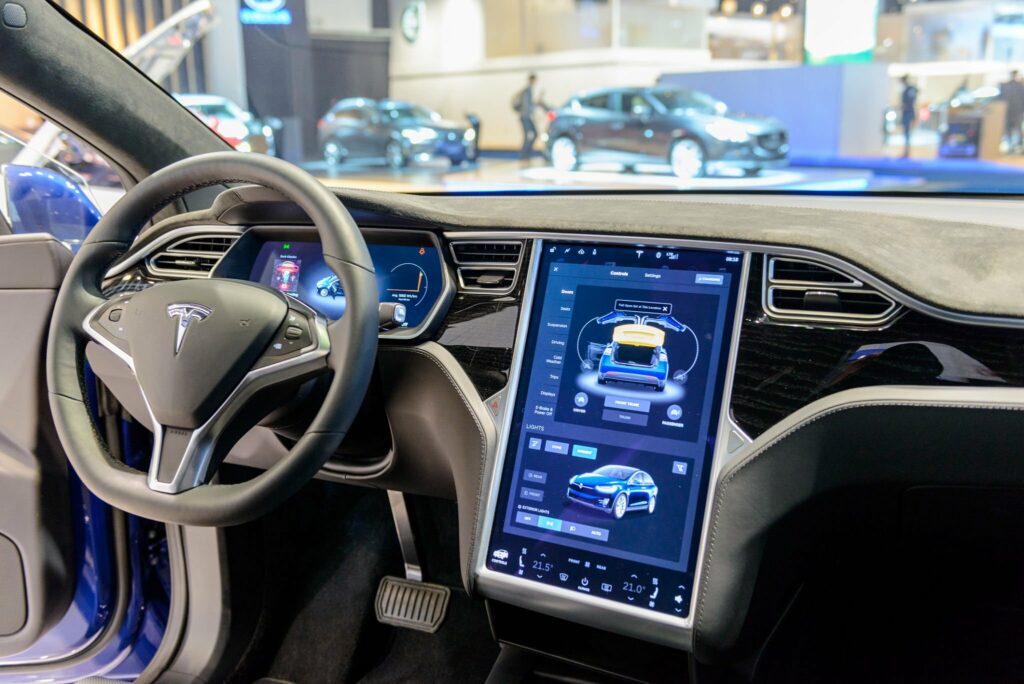